Electric Vehicle Research System
Experience the advanced Electric Vehicle Research System for accurate hardware-level simulations.
Innovative Electric Vehicle Research Solution
Electric vehicles (EVs) are reshaping the global market with their promise of sustainability, lower operating costs, and technological innovation. However, there remains a significant skills gap in the workforce, which often lacks practical, comprehensive training in EV systems.
MatView’s EVRS is designed specifically for universities and educational institutions to address this challenge. It provides hands-on experience and deep understanding of the following key EV components:
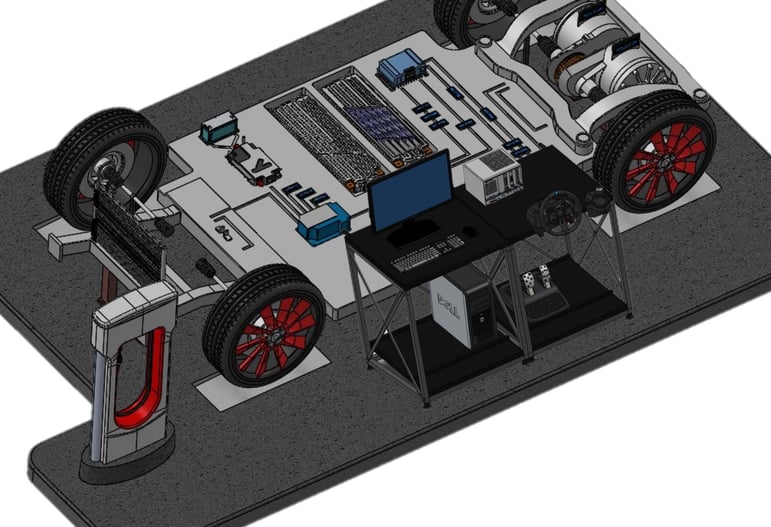
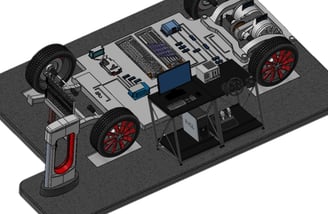
Battery Technology
Drive Train Technology
Charging Technology
Power Electronics
Drive Cycle Simulations
Vehicle Dynamics
Research and Experimentation Opportunities
A. Battery Systems
Analyze charging and discharging characteristics under different modes.
Evaluate state-of-health and lifespan across various cycles.
Conduct performance testing aligned with international standards.
B. Drive Cycle Simulations
Study speed-torque characteristics, motor efficiency, and dynamic performance.
Test regenerative braking and heating characteristics.
Simulate different drive cycles, including Indian Drive Cycle (IDC) and New European Driving Cycle (NEDC).
C. EV Drive Line
Develop and test control algorithms for power converters and inverters.
Analyze energy efficiency during varying loading and drive cycle conditions.
D. EV Charging Systems (Modular and Adaptive EVSE)
Evaluate charging behavior with onboard and offboard chargers.
Investigate fast charger communication protocols like GB/T, CCS, and CHAdeMO.
EVRS Key Features
Comprehensive Learning
EVRS covers all critical aspects of EV technology, ensuring a holistic educational experience.Integrated Learning Environment
Features a modular car chassis with real EV components for practical, hands-on training.Real-Time Simulations
Utilizes actual EV parts for accurate testing and research.Customizable Control
Includes open-source software to modify control algorithms and techniques.
Central Control and Monitoring Unit
Experience hardware in loop simulations Using NI PXI Controller on NI LabView User Interface.
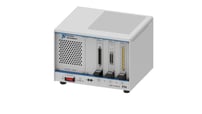
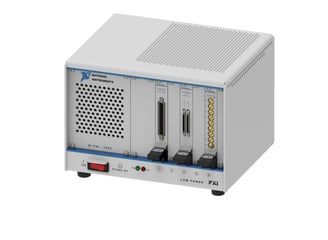
The Central Control Unit (CCU) is the core of the Electric Vehicle Research System (EVRS), designed to ensure seamless integration and efficient operation of all EV components. It acts as the brain of the system, managing and monitoring various subsystems in real-time.
Key Features
Real-Time Monitoring
Tracks performance metrics of all EV subsystems, including motors, batteries, chargers, and power electronics.
Provides real-time data visualization for enhanced understanding and analysis.
Comprehensive Integration
Communicates with all critical EV components, such as the Battery Management System (BMS), DC/DC converters, motor controllers, and charging systems.
Ensures seamless interaction and synchronization of all subsystems.
Customizable and Open-Source Platform
Built on an open-source architecture to allow customization of control algorithms.
Enables users to develop and test their own solutions tailored to specific research needs.
Data Logging and Analysis
Logs experimental data for further analysis, enabling students and researchers to identify trends, optimize performance, and validate their findings.
Supports exporting data in graphical and dataset formats for detailed reporting.
Safety and Reliability
Integrated with advanced safety protocols to monitor and mitigate risks during testing and operation.
Ensures stable operation under varying conditions.
User-Friendly Interface
Intuitive interface for controlling and managing all EV subsystems.
Compatible with tablets and mobile devices for remote access and control.
Benefits for Research and Education
Hands-On Learning: Enables students to interact with all components of an EV system in a controlled environment.
Enhanced Experimentation: Allows users to test various configurations and algorithms without hardware limitations.
Real-World Application: Prepares students with practical knowledge for careers in the EV industry.
Scalable Design: Adapts to new technologies and educational needs over time.
The CCU bridges the gap between theoretical knowledge and practical application, making it an indispensable tool for EV research and education.
Experience cutting-edge hardware-level simulations with our sophisticated Fast Charger up to 40kW.
AC to DC Fast Charger
The AC to DC fast charger is designed to rapidly and efficiently charge EV batteries, adhering to global standards for fast charging protocols.
Key Features:
High Efficiency: Converts alternating current (AC) to direct current (DC) with minimal energy loss.
Standards Compliance: Supports fast-charging protocols like GB/T, CCS, and CHAdeMO.
Dynamic Current Adjustment: Automatically adjusts output current based on the battery's charging state.
Safety Mechanisms: Includes overvoltage, overcurrent, and thermal protection for safe operation.
Real-Time Communication: Interfaces with the EVSE and vehicle BMS for optimized charging cycles.
Compact Design: Ideal for research labs and educational setups.
Motor-Dynamo Set
The motor-dynamo set is a versatile component used for energy regeneration, testing, and system analysis.
Key Features:
Energy Regeneration: Functions as a generator to simulate regenerative braking and analyze energy recovery.
Load Testing: Provides variable load conditions to test the performance of propulsion motors.
High Efficiency: Achieves up to 92% efficiency for reliable experimentation.
Thermal Management: Features internal fan cooling to maintain optimal operating temperatures.
Flexible Testing Capabilities: Supports speed-torque analysis, friction torque evaluation, and dynamic performance testing.
Robust Design: Built to handle continuous operation under demanding conditions.
Onboard Charger
The onboard charger is a critical EV component that facilitates efficient and safe battery charging using AC power.
Key Features:
Integrated Design: Compact, lightweight charger installed directly in the EV system.
Multi-Mode Charging: Supports Constant Current (CC) and Constant Voltage (CV) charging modes.
Wide Voltage Range: Operates across a broad range of input voltages (90V to 230V AC).
High Efficiency: Achieves efficiency levels of up to 90%, ensuring minimal energy loss.
Communication Protocols: Interfaces with the BMS for optimal charging management.
Safety Measures: Includes protections against overvoltage, overcurrent, and overheating.
Lithium Iron Phosphate (LFP) Battery
The LFP battery is a reliable and durable energy storage solution, widely used in EV systems due to its superior safety and longevity.
Key Features:
High Thermal Stability: Resistant to thermal runaway, making it safer for EV applications.
Long Cycle Life: Capable of over 3,000 charge-discharge cycles at 80% Depth of Discharge (DoD).
Enhanced Energy Density: Offers balanced specific energy and power for efficient performance.
Broad Operating Temperature Range: Functions effectively between -20°C and 55°C.
Fast Charging Capability: Supports higher charging currents for reduced charging time.
Eco-Friendly: Uses non-toxic materials, making it a sustainable choice.
These components collectively provide the foundation for comprehensive research, development, and education in EV technology.
LFP Battery
Motor-Dynamo Set
On Board Charger
Dynamo Converter
Other Components
DC to DC Converter
Charging Gun
Charging Gun Female Port
Meters
Auxiliary Battery
AC Motor Converter
Contact Us for Electric Vehicle Research System
Reach out to us for any questions or inquiries about our sophisticated wind turbine emulator system. We are here to assist you with hardware-level simulations and more.
Get in Touch
02975-356173
Message
info@matview.co.in